Entenda o que é MRP, como funciona e quais os seus benefícios para o planejamento de necessidades de materiais nas empresas.
O MRP (Material Requirements Planning, ou Planejamento de Necessidades de Materiais) é uma metodologia fundamental para qualquer empresa que deseje otimizar a produção, garantir disponibilidade de insumos no momento certo e reduzir desperdícios.
A gestão inteligente de estoques e insumos pode determinar a competitividade do negócio, sobretudo em tempos de grande concorrência e consumidores exigentes.
Neste artigo, vamos explorar desde a definição do MRP, suas etapas de funcionamento, os benefícios que traz ao ambiente corporativo, até a comparação com outros sistemas de planejamento e dicas de implementação.
Se a sua empresa lida com produção, montagem ou qualquer processo que envolva múltiplos componentes, o MRP se mostra um aliado estratégico para o sucesso.
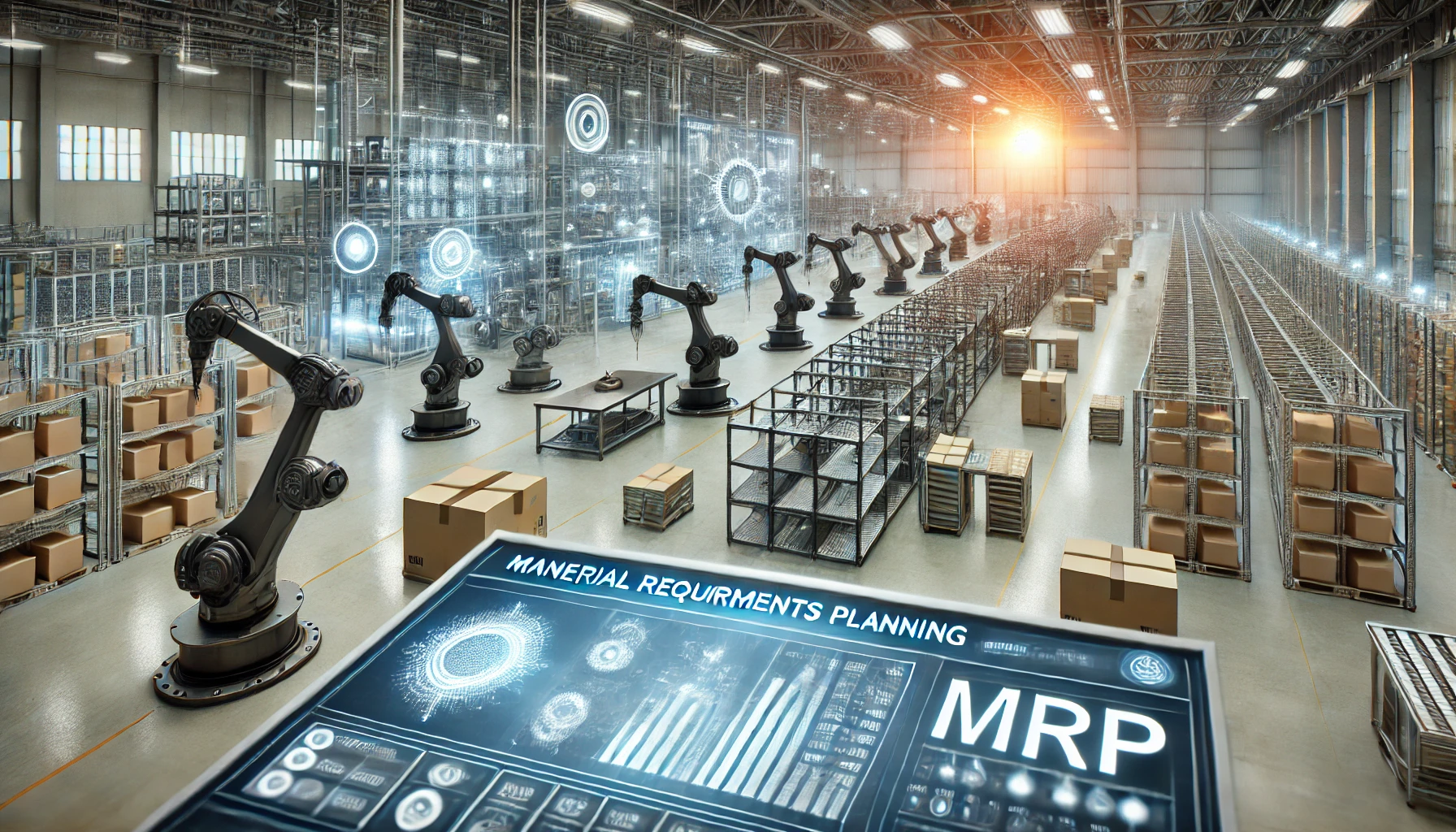
O que é o MRP (Planejamento de Necessidades de Materiais)?
O MRP (Planejamento de Necessidades de Materiais) é uma técnica de gestão e planejamento que surgiu com o objetivo de determinar quantos materiais e componentes devem ser comprados ou produzidos, em que momento, e em que quantidade, para atender ao plano de produção de uma empresa.
Em outras palavras, o MRP ajuda a responder à pergunta central: “O que preciso comprar ou fabricar para produzir meus produtos na data certa, evitando faltas ou excessos de estoque?”.
Definição de MRP e sua importância na gestão de recursos
O conceito do MRP está diretamente relacionado ao controle de estoques. Ele calcula, a partir de uma previsão ou de pedidos firmes, o cronograma de produção ou aquisição de cada item necessário.
Dessa forma, busca equilibrar oferta e demanda de insumos, garantindo que não se acumulem materiais sem uso e que não faltem insumos essenciais na hora de fabricar.
Esse equilíbrio se traduz em menor imobilização de capital e redução de desperdícios, com impactos positivos no fluxo de caixa.
Ao aplicar o MRP, a empresa melhora a forma como gerencia seus recursos, pois cada requisição de compra ou de produção interna é planejada com antecedência.
Na prática, isso não apenas evita a ruptura de estoques e atrasos nos pedidos de clientes, mas também minimiza custos de manutenção de inventário, que podem ser bastante onerosos se o nível de estoque for exagerado.
Como o MRP se relaciona com o processo de produção
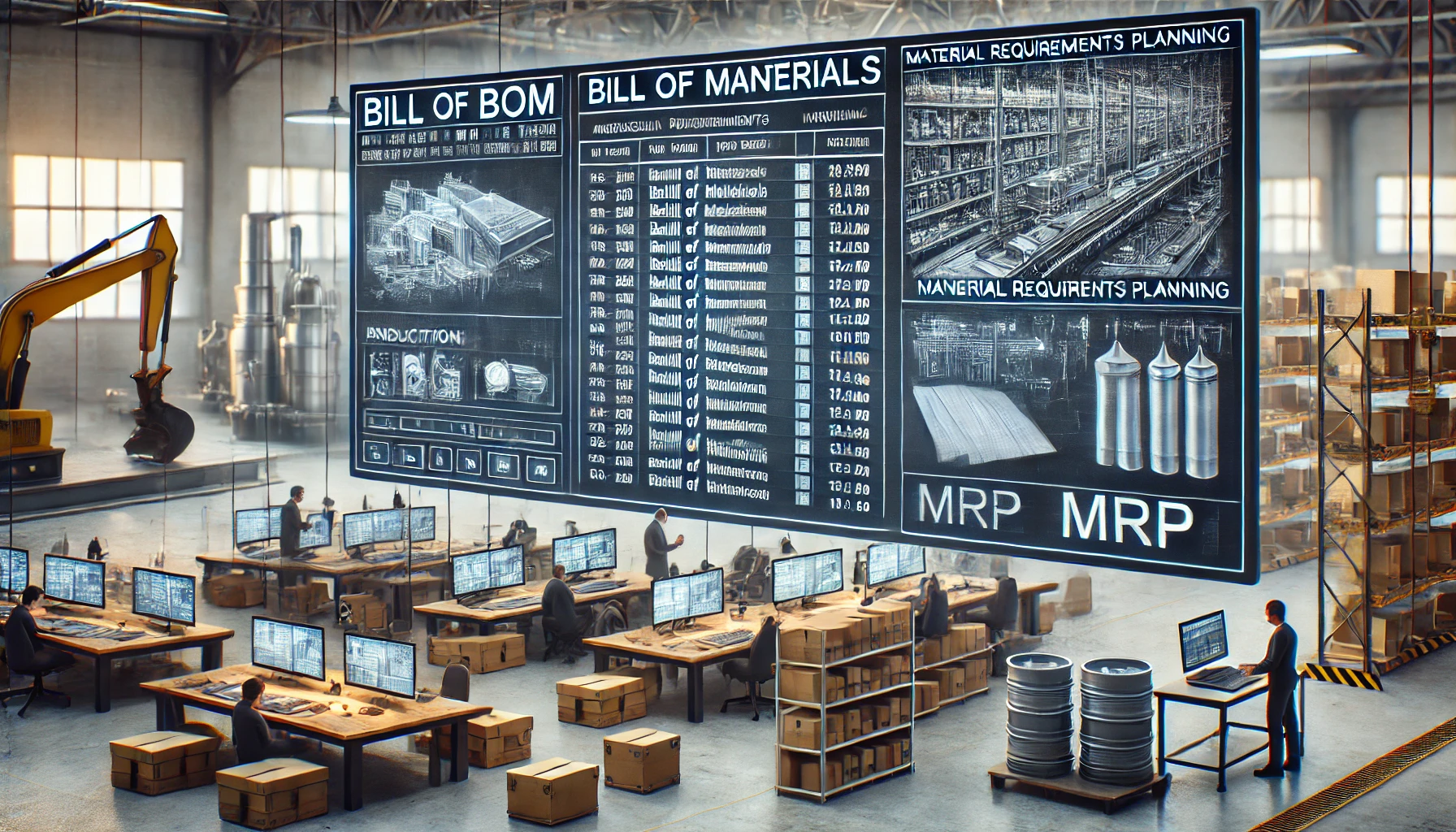
Em um processo produtivo típico, há uma lista de materiais (BOM, Bill of Materials) que define todos os componentes necessários para fabricar o produto final.
O MRP cruza essas informações com a agenda de produção (ou a projeção de demanda) e com os saldos atuais de estoque, gerando recomendações de compras e ordens de produção internas.
Ele ainda considera o lead time — tempo desde o pedido de compra até a entrega efetiva — bem como quantidades mínimas de pedido e tamanhos de lote, resultando em um planejamento de materiais bem alinhado com o cronograma produtivo.
Como funciona o MRP no planejamento de materiais?
Para quem não conhece, o MRP funciona como um “cérebro” de necessidades de suprimentos.
Ele utiliza dados como lista de materiais, status do inventário e previsão de vendas para emitir sugestões de compra ou ordens de produção. Esse processo segue algumas fases:
Etapas do processo de MRP: do pedido à entrega:
- Entrada de demanda: Podem ser pedidos firmes de clientes ou previsões de vendas para determinado período.
- Explosão da lista de materiais: O sistema de MRP identifica cada item necessário para fabricar o produto final, verificando quantidades e subcomponentes (itens de nível inferior).
- Verificação de estoque atual: Consulta-se o estoque disponível de cada item, incluindo eventuais pendências de entrega ou ordens de produção em andamento.
- Cálculo das necessidades líquidas: Determina-se quantas unidades realmente precisam ser compradas ou produzidas, levando em conta o estoque e itens já encomendados.
- Emissão de requisições: O MRP sugere ordens de compra de matérias-primas e ordens internas de produção, considerando datas de início, quantidades e lead time.
- Acompanhamento e execução: A equipe de compras envia os pedidos aos fornecedores, enquanto a produção inicia as ordens internas no prazo ideal.
A integração entre MRP e outros sistemas de gestão (como ERP)
O MRP funciona melhor quando integrado a outros sistemas de gestão, como ERP (Enterprise Resource Planning).
Em muitos ERPs, o MRP é um módulo interno, enquanto algumas empresas adotam sistemas MRP independentes que se conectam ao software de vendas, estoque e finanças.
Essa integração é importante para que as informações de pedido de venda, estoque e financeiro estejam atualizadas em tempo real, permitindo ao MRP emitir ordens coerentes com a situação atual do negócio.
Exemplo prático de aplicação do MRP no controle de estoque
Imagine que uma empresa fabrique computadores. O MRP analisa quantas placas-mãe, processadores e componentes menores estão disponíveis e quantos são necessários para atender à previsão de produção do mês.
Se faltam 500 placas-mãe para cumprir um lote, o MRP gera uma ordem de compra. Tudo isso evita a aquisição exagerada de componentes caros ou a falta de material, o que paralisaria a linha de montagem.
Esse mesmo modelo de funcionamento se aplica a setores diversos, como automotivo, alimentício e têxtil, pois o MRP é universal na lógica de planejar necessidades.
Benefícios do MRP para a sua empresa
Adotar o MRP traz uma série de vantagens que vão além da simples organização de matérias-primas.
Os ganhos se refletem em aspectos financeiros, operacionais e de relacionamento com clientes e fornecedores. Destacamos alguns benefícios:
- Redução de custos com inventário e desperdício:
Manter estoques excessivos gera custos de armazenagem, seguro, perdas por obsolescência ou validade.
Com o MRP, a empresa compra e fabrica na medida certa, reduzindo capital parado em estoque e limitando o desperdício. Em muitos casos, os resultados no fluxo de caixa são imediatos, pois menos dinheiro fica imobilizado.
- Aumento da eficiência e precisão no processo produtivo:
O MRP assegura que os insumos cheguem na hora exata, ajustando a produção a partir de cronogramas realistas.
Com tudo no lugar certo no momento certo, a fábrica ou a linha de montagem evita interrupções e retrabalhos, elevando a produtividade.
O monitoramento contínuo do MRP ainda permite identificar gargalos e ajustar prazos com antecedência.
- Melhoria no atendimento ao cliente e na previsão de demanda:
Como o MRP trabalha com previsões de venda (ou pedidos firmes), ele contribui para fornecer prazos de entrega precisos.
Ao saber que os insumos estarão disponíveis e que as fases de produção não serão interrompidas, a empresa pode comprometer-se com datas de entrega mais confiáveis. Os clientes notam essa pontualidade, reforçando a reputação do negócio.
- Como o MRP contribui para a sustentabilidade e otimização de recursos:
Ao planejar adequadamente, a empresa evita compras desnecessárias, reduz o uso de embalagens, minimiza resíduos de produção e até economiza energia em processos que não precisarão rodar com tanta folga.
Implementação do MRP: Como adotar na sua empresa?
Ter um bom entendimento de como o MRP se encaixa no contexto produtivo é o primeiro passo. Entretanto, a implementação requer cuidados e etapas bem definidas:
Dicas para implementar o MRP de forma eficiente:
- Mapeie o processo atual: Entenda como sua empresa lida com pedidos, compras, estoque e produção. Identifique gargalos e falhas de comunicação.
- Crie ou revise a lista de materiais (BOM): Cada produto deve ter mapeados todos os componentes necessários, inclusive quantidades e níveis de subcomponentes.
- Estabeleça prazos e lotes mínimos: Determine os lead times e o tamanho mínimo de compra ou de produção, pois isso afeta o cálculo do MRP.
- Integre sistemas: Conectar o MRP com o módulo de vendas e estoque (ou com um ERP completo) é crucial para manter dados sincronizados.
- Treine a equipe: O envolvimento dos times de compras, produção e logística garante adoção efetiva e correções rápidas de qualquer problema no fluxo.
Ferramentas e softwares de MRP recomendados
Há soluções específicas para MRP, como softwares voltados à manufatura, e módulos de ERP que já incluem o MRP integrado. Exemplos incluem:
- SAP;
- Oracle;
- Totvs;
- Microsoft Dynamics;
- Entre outros.
O melhor é analisar o porte da empresa e a complexidade de sua produção para escolher uma ferramenta escalável e que não seja excessivamente cara ou complexa.
Superando os desafios na implementação do MRP
Resistência a mudanças, dados inconsistentes e falhas na atualização do estoque são alguns obstáculos comuns.
É preciso garantir que cada etapa do processo seja revisada, que haja disciplina no registro de entradas e saídas e que haja comunicação fluida entre os setores.
MRP x outros sistemas de planejamento: qual é a melhor opção?
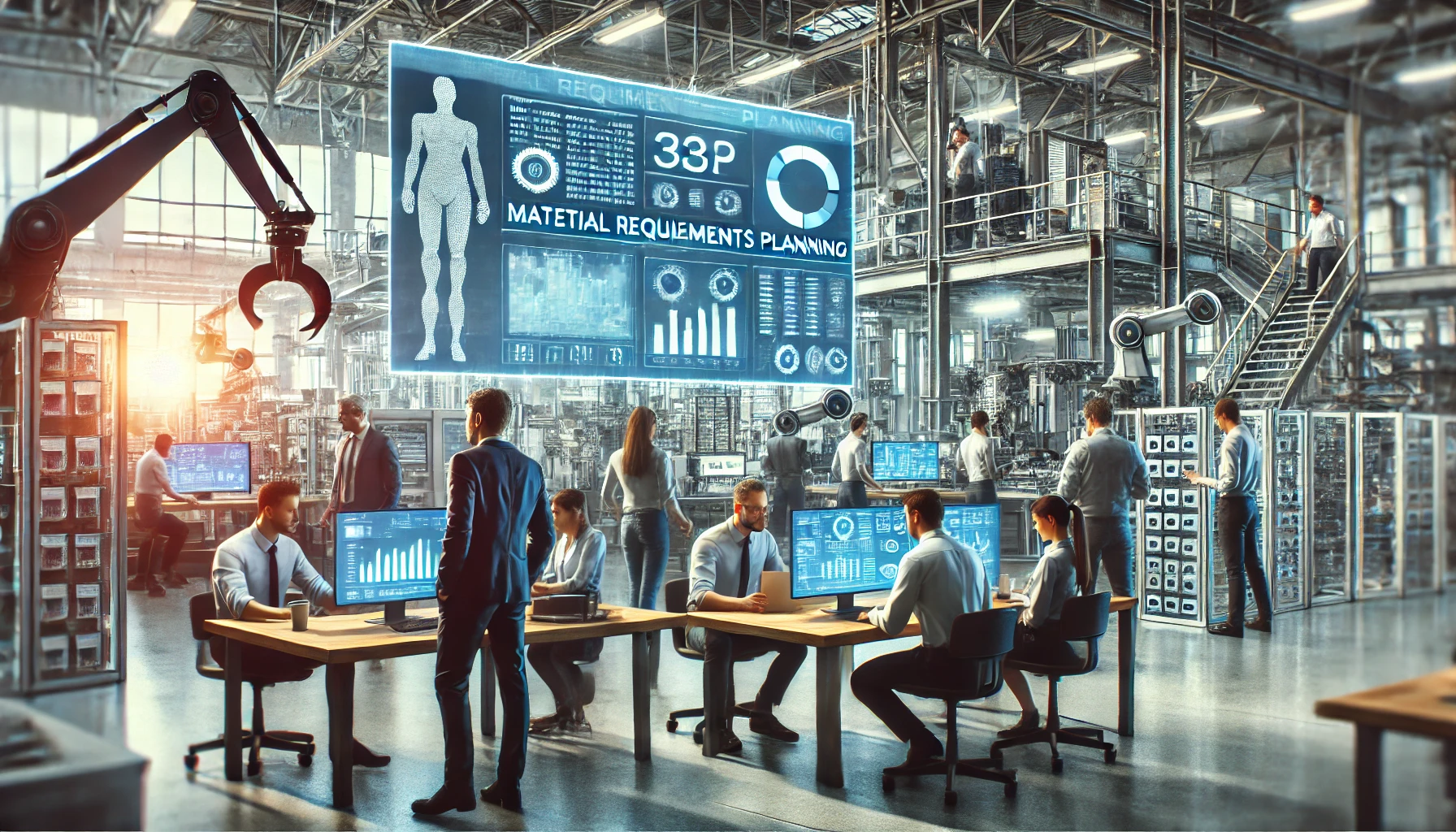
O MRP é um método clássico e bastante consolidado, mas não é a única forma de planejar suprimentos e produção.
Existem outros sistemas e metodologias, como APS (Advanced Planning & Scheduling) ou a simples adoção do ERP sem o módulo de MRP tradicional.
Comparando MRP com sistemas como ERP e APS:
- ERP: O Enterprise Resource Planning é um sistema de gestão integrado que abrange finanças, vendas, compras, estoque, RH, etc. Ele pode ter módulo de MRP interno, mas nem todo ERP entrega as funcionalidades profundas de planejamento de necessidades.
- APS: Advanced Planning & Scheduling geralmente funciona de modo mais sofisticado que o MRP, levando em conta múltiplos recursos (máquinas, mão de obra) e otimização simultânea. É comum em fábricas complexas.
Quando optar por um MRP e quando escolher outra solução de planejamento
O MRP é altamente indicado para empresas que fabricam produtos com lista de materiais definidas, que precisam planejar a compra e a produção de insumos em função da demanda.
Para situações em que a produção é extremamente complexa e envolve múltiplas restrições de capacidade de máquinas, o APS pode ser mais adequado.
Já se a empresa deseja um pacote integrado de gestão, mas sem refinamentos profundos em planejamento de insumos, um ERP com módulo de planejamento básico pode bastar. O importante é avaliar o nível de detalhamento e automação requeridos.
Conclusão
O MRP (Planejamento de Necessidades de Materiais) se mostra um recurso valioso para empresas que lidam com produção ou montagem de produtos, garantindo a disponibilidade dos insumos certos, no momento certo, na quantidade adequada.
Ao adotar o MRP, é possível minimizar custos de estoque, evitar paradas de produção por falta de componentes e proporcionar maior confiabilidade de prazos ao cliente.
Integrado a sistemas de gestão (ERP) e aliado a boas práticas de gestão e treinamento das equipes, esse método traz benefícios tangíveis em eficiência, redução de desperdícios e sustentabilidade.
Veja também: